What is it?
Mineral Composite Fiber Reinforced Block system using molded blocks that interlock like LEGO bricks to create entire structures. Renco’s proprietary MCFR combines repurposed glass fibers, recycled plastic, resin, and limestone into a powerful composite that is pound for pound stronger than concrete, extremely economical, and finishes in a fraction of the time.
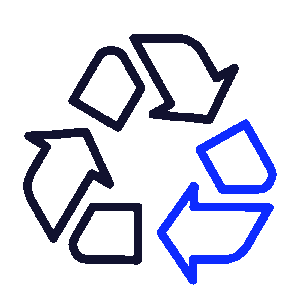
How is it made?
Using compression molding and the pultrusion process, any shape necessary may be formed from the composite compound (blocks, roof beams, joists, or flooring). The MCFR is fused with a methyl methacrylate bonding agent that is used in the trucking, aerospace, and marine industries.
What sizes are offered?
- Residential blocks: 6” wide x 8” high, available in 3”, 6”, 12”, and 30” lengths.
- Commercial blocks: 8” wide x 8” high, available in 4”, 8”, 16”, and 32” lengths.
How are the blocks installed?
Chromatic Installation Plans make constructing a building with RENCO blocks a streamlined and accessible process using color-coded assembly schematics and proprietary adhesives to build a monolithic structure in a fraction of the time.
An innovative building system allows for adaptability, accommodating various types and sizes of interlocking units.
The proprietary MCFR weaves together recycled glass fibers, recycled plastic, resin, and stone into a composite that is 23 times stronger than concrete.
Made with natural, recycled materials producing a lower carbon footprint and minimal waste. No need for on-site cutting or dumpsters.
Blocks weigh similar to a wood structure and are 9%-18% the weight of concrete.
Able to withstand forces of Category 5 hurricane wind loads. Passed rigorous ASTM and TAS standards.
Inherent water barriers. Mold, mildew, rot & corrosives resistant (ASTM testing-backed assurance).
Easy installation for varying levels of skill and expertise. Only supplied materials and “Build by Color” assembly schematics are required. No heavy equipment is needed, only proprietary adhesive.
Faster, less costly to build than comparable wood, concrete, and steel buildings. Self-supporting. No framing, shoring, bracing or waiting for related trades/inspectors.
Fire resistant (exceeding requirements with successful 1 and 2-hour rated fire rating tests).
No maintenance post-construction; proven by 8+ years of rigorous testing across the U.S., and hundreds of individual tests conducted in 10 States.
Pest and termite resistant. No cellulose or other food sources for insects such as termites (ASTM testing-backed assurance).
It is resistant to earthquake, and snow loads. Currently approved for Seismic Design Categories (SDC) A and B.


10+ YEARS IN THE MAKING
Perfecting the Most Disruptive Innovation in Construction in over 100 Years.
Exclusive Patents
Extensive evaluation under IBC and IRC. Comprehensive testing of materials, connections, assembly, fire, sound, thermal, and environmental aspects.
440 ANSI Certified
Completed and Passed.
100+ Years in the Industry
The fusion of time-tested expertise and a pioneering vision.
Manufacturing Location
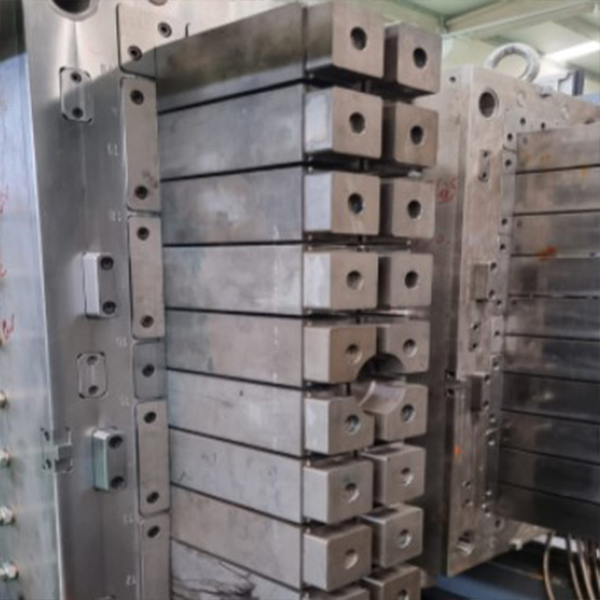
Manisa, Turkey
An impressive 280,000 sq. ft. facility that operates on a turnkey model, integrating automation and proprietary equipment. This revolutionary approach ensures that every aspect of the warehouse process is meticulously optimized, setting new standards in the industry.
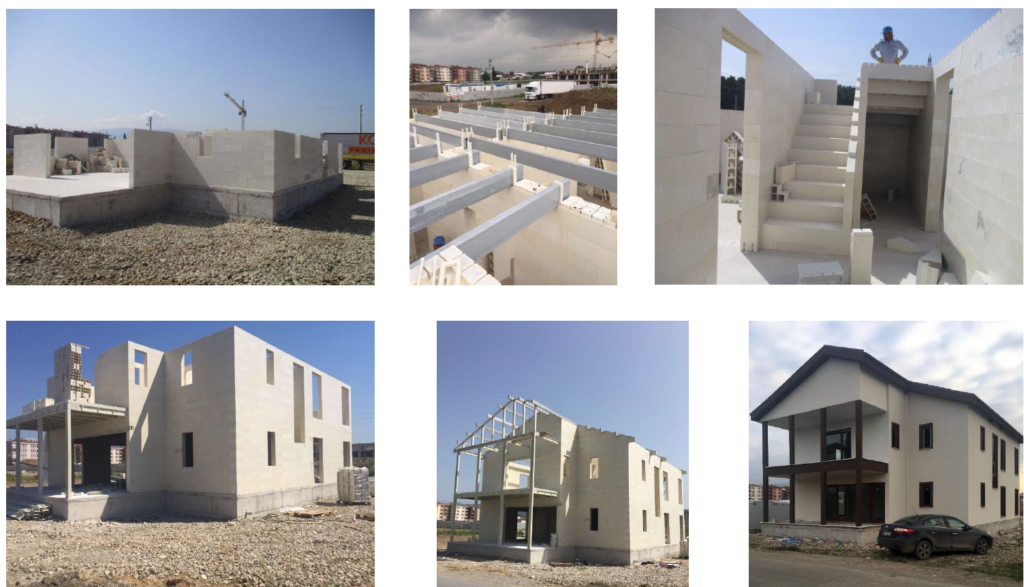
Affordable
Affordable, attainable and workforce housing, emergency response construction.
Multi-Family
Apartments, condominiums, townhomes, hotels, and motels up to five stories (higher stories can be achieved with concrete block ground level).
Single-Family
One-story and multi-story single-family.
FAQ
General Questions
Yes. This can be done in design phase and pre-cut during manufacturing, or the ceiling height can be dropped to accommodate as it was done at Lakewood Village. Openings can also be cut in the middle third of joists on-site, if required.
The block has an R-value of 2.2. Thermal conductivity coefficient=0.05 w/MK TS825.
This depends on wind loading. In Florida's High Velocity Hurricane Zone it can go up to 10' unbraced.
No. It goes on top of that wall height.
Joists run parallel with a double or single loaded corridor.
Composite window bucks are provided to affix doors, windows, and sliding glass doors.
Joists are adhesively joined to the walls forming moment connections. Floor and roof deck are mechanically fastened to the joists and a ledger block at the top of each wall.
Depends on the soil, but similar to wood load. Lakewood Village has 3-story buildings; and the geotechnical report indicated soil capacity at 2500 psf. The slab on-grade was 4" thick with 6 x 6 welded wire fabric, and was depressed an additional 12" under bearing and shear walls. Two No. 5 rebars were inserted at the bottom of each depression.
Bolts are located based on wind-loading. Bolts are 4" x 1/2" diameter galvanized Titan HD’s. At Lakewood Village they were installed approximately 24" on-center.
Balconies are 4" lower in elevation. Cant strips are used to promote positive drainage.
Depends on spacing of beams per engineer design and building type. Lakewood Village was designed using a live-load of 40 psf plus a dead load of 20 psf and a superimposed dead load of 20 psf.
All sizes fit inside the 6" residential blocks. For 8" commercial blocks, it is furred out like concrete block construction.
Yes, with additional support to accommodate this additional load and must be designed for load.
Yes, but must be engineered, as the bearing walls of the apartments will most likely not align with those of garage.
It is not affected by ultraviolet rays. ASTM-D 4329 and ASTM-G-53.
Less dumpsters, reduction of insurance build risk, a shortened build time, less skilled trades needed.
Apply paint and coating directly. The walls are monolithic elements; no plaster is required. No mortar lines means a smooth surface.
See IAPMO UES ER-508. It has passed and been approved.
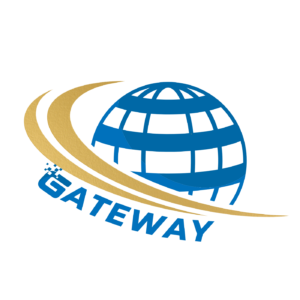
SUSTAINABLE BUILDING COMPANY
Supplies Sustainable Technologies, Consulting, and Construction Services for Our Clients
Main Office
- +1.225.303.6077 | 888.772.5333 ext .1
- 1349 West Peachtree Street Northeast Atlanta, Georgia 30319 USA
Houston
- +1.604.819.9069
- 801 Travis Street Houston, Texas 77002
Miami
- +1.903.482.5172
- 66 West Flagler Street Miami, Florida 33130
Contact Us
We Would Be Happy To Hear From You
Meetings acceptable by appointment only
- +1.225.303.6077 | 888.772.5333 ext .1
- robert.jackson@gateway2cap.com
- 1349 West Peachtree Street Northeast Atlanta, Georgia 30319 USA